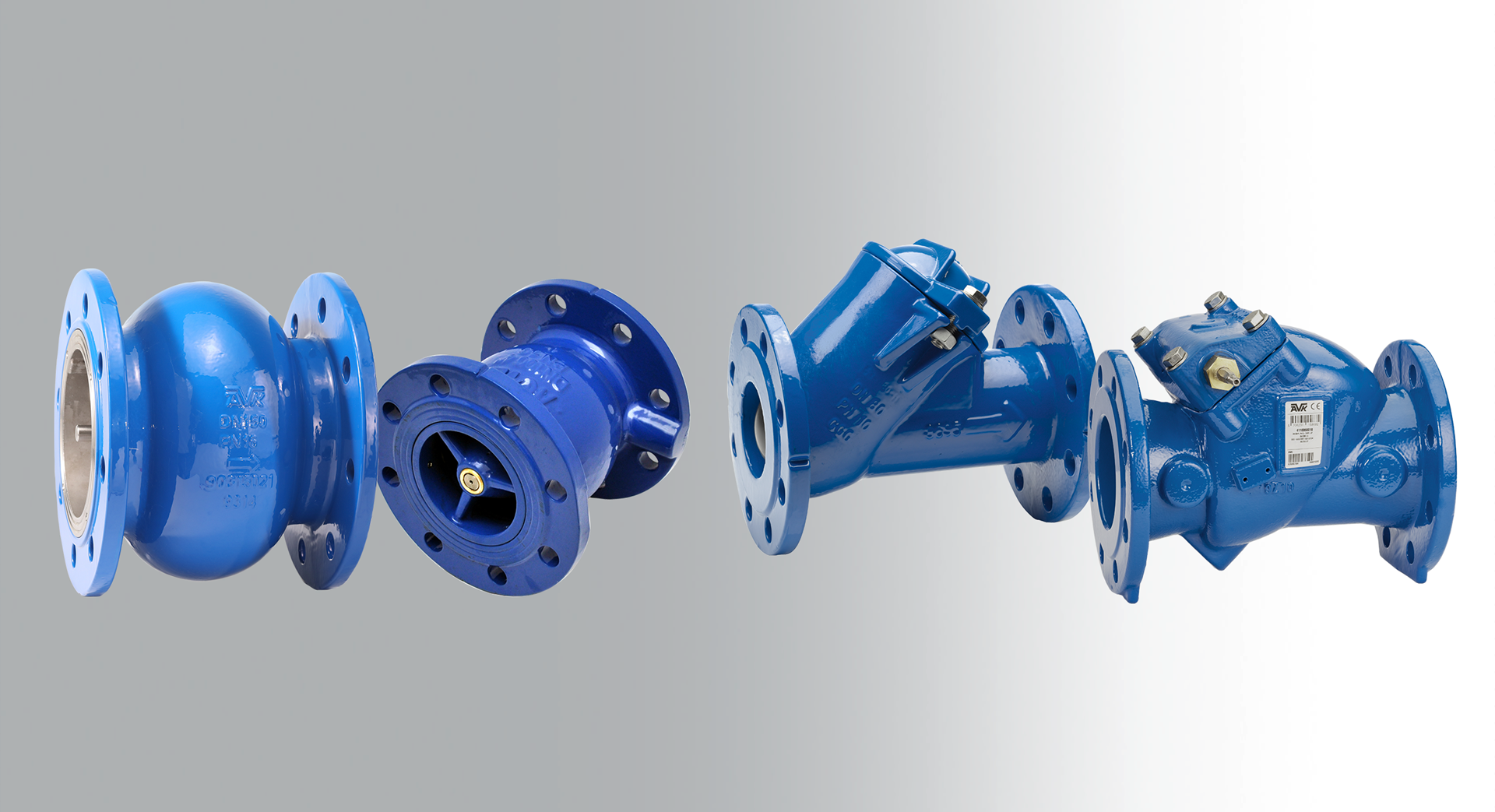
How to choose the right check valve
Choosing the right check valve is essential to achieve an efficient and reliable performance while minimising energy consumption. See the types of check valves and key factors to consider for your application.
Types of check valves
Selecting the correct type, size and specification of check valve depends on the operating conditions and it is important to ensure smooth, trouble-free and long-term operation with low energy consumption. While standard check valves are sufficient for many systems, pumping systems often require a careful selection of the correct check valve to ensure optimum operation and address backflow problems.
Ball check valves
In general, ball check valves are simple and cost-effective. Their compact design and lack of external parts make them both affordable and highly reliable. However, they do not have an open/close indicator, which can be a disadvantage in certain applications.
Due to their smooth bore design, ball check valves are often used in wastewater applications. The full and smooth bore ensures full flow, preventing solid deposits from forming on the bottom of the valve. In addition, the self-cleaning mechanism of the rotating ball eliminates the risk of impurities getting stuck to the ball.
For more information, visit our page about ball check valves.
Swing check valves
Swing check valves are the most common type of non-return valve. They are inexpensive and operate entirely on flow and pressure, requiring no external energy or control. Swing check valves are available with open/close indicators and can be equipped with a lever and weight or a lever and spring for visual monitoring, or with devices that allow digital feedback.
The design of the swing check valve provides a full bore opening, which minimizes pressure loss. Swing check valves are ideal for systems with a low risk of pressure surges. Due to their design, they are often used in water and wastewater applications.
For more information, visit our page about swing check valves.
Nozzle check valves
In the design of "Nozzle" check valves (spring loaded check valves) the valve disc is connected to the stem which moves along the central horizontal axis. A spring is placed between the disc and the diffuser sleeve. When flow enters the check valve, the hydraulic force applied to the front reacts against the spring, compressing the spring and allowing the check valve to open. When the flow stops, the spring forces the disc to return to the closed position.
Due to the spring assisted closure and short linear valve stroke, the nozzle check valve is one of the fastest acting check valves available and is often used in pump systems where water hammer is a potential problem. The disc is constantly in the direct flow line, which can result in a slightly higher pressure drop compared to a standard check valve.
For more information, please visit our product page nozzle check valve
What to consider when selecting your check valves?
Choosing the ideal check valve for your application depends on several selection criteria. Not one type of check valve suits every situation, and the factors listed below are essential to consider. However, not all of them are equally important for all applications. By evaluating these factors in relation to your system requirements, you can select a check valve that will ensure reliable performance, minimal maintenance, and long-term operational efficiency.
Fluid Compatibility
All check valves referred to in this article are designed for water and treated wastewater applications. However, in raw wastewater/sewage applications, the presence of solids can affect the performance of the valve, requiring careful consideration of design and material compatibility.
Flow characteristics
Fast closing of a check valve can protect upstream equipment, such as pumps, from damage. However, fast closing will not protect against pressure surges caused by starting and stopping pumps. When the valve opens (and closes) rapidly, the flow will change rapidly and thus increasing the likelihood of pressure surges. Consider the flow dynamics of your system to select a valve that effectively reduces these risks.Pressure loss
Pressure loss is influenced by fluid velocity and valve design. Valves with unrestriced opening minimize pressure drop, while designs with narrower bores increase fluid velocity and, consequentely, pressure drop. There are different values for pressure loss, including zeta values, Kv and Kvs values.
Total cost of ownership
The total cost of your check valve can be more than just the initial purchase price. Long-term costs such as maintenance, energy costs and equipment protection (for examples pumps) can be as important, if not more important, than the initial purchase price and installation costs.
In general, the simpler the valve design, the lower the maintenance requirements. The higher the Kv value, the lower the energy consumption. The higher the performance, the better the protection capacity.
Non-slam characteristics
Closing a check valve can affect pressure surges. First, when the pump stops, starting the pressure surge. Second, when the flow reverses and hits the fully closed check valve. If the check valve closes too quickly, the kinetic energy is converted into high pressure, which stresses the pipes and creates a lot of noise.
A slam sounds as if the disc or ball of the check valve is hitting the seat. This can make quite a noise. However, the sound is not caused by the physical closing, but by a sound wave created by a pressure peak that stretches the pipe wall.
To prevent the occurence of check valve slams, the check valve should close in a controlled manner and the closing should be slowed further when the valve is almost closed. This requires additional auxiliary equipment such as hydraulic dampers, which act as a cushion for the check valve as it approaches its closed position. The controlled closing allows the fluid to pass through the check valve until it closes, which results in less kinetic energy being converted into high pressure, and therefore less energy to feed and maintain the pressure wave.
Swing check valves have the disc in the direction of flow, which helps to close quickly and therefore have non-slam characteristics. However, many pumps today have frequency converters, which allow them to adjust the start-up and closing time to prevent or minimize the risk of water hammer.